Oke Shibori
- 京都絞り工芸館
- Sep 6, 2021
- 3 min read
Updated: Dec 3, 2021
The Oke shibori technique is used when dyeing large patterns etc. The tub is made of cypress. The part of the fabric to be dyed left placed outside over the edge of the tub, and the part to be undyed is placed in the tub, and the top and bottom lids are closed tightly and the whole tub is dyed.
This 'Oke shibori' is used to dye the sky part of the huge silk screens 'Fine Wind, Clear Morning'.
The sky part is placed outside of the tub and the Mt. Fuji part is placed in the tub.
A total of 6 pieces of fabric are placed, 2 on each side of the first tub and 2 on one side of the second tub.
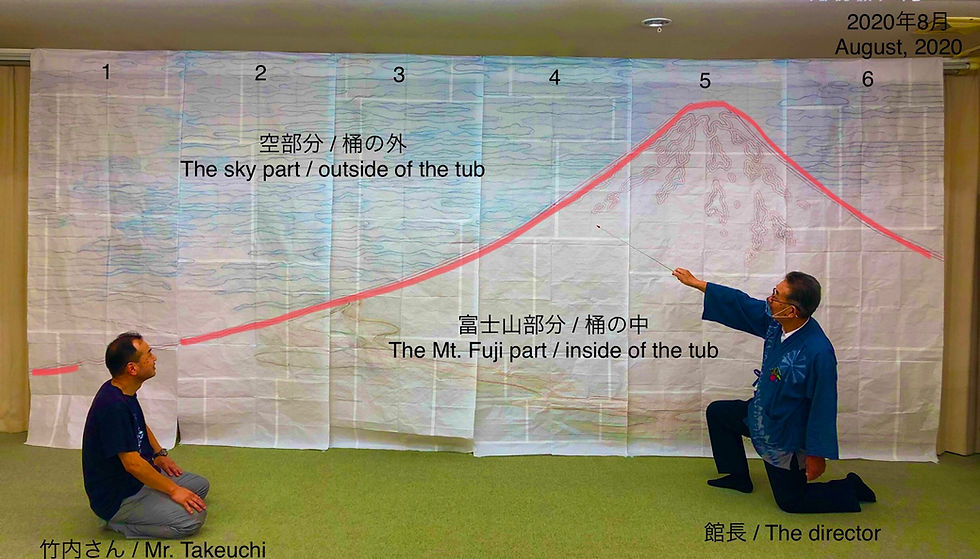
Explanations using the sketch(paper)

After completion
Usually, the shibori craftsman dose the shibori work at home, but this time he brought a set of tools that he always uses to the Kyoto Shibori Museum and cooperated with the shooting.
The craftsman who visited this time is Mr. Nagatani san, an expert who has 50 years of experience as a oke shibori craftsman.
The tub used is 36 cm in diameter and has been used for over 30 years.
Hinoki (cypress) is resistant to heat and water, and can be used for a long time with proper maintenance.
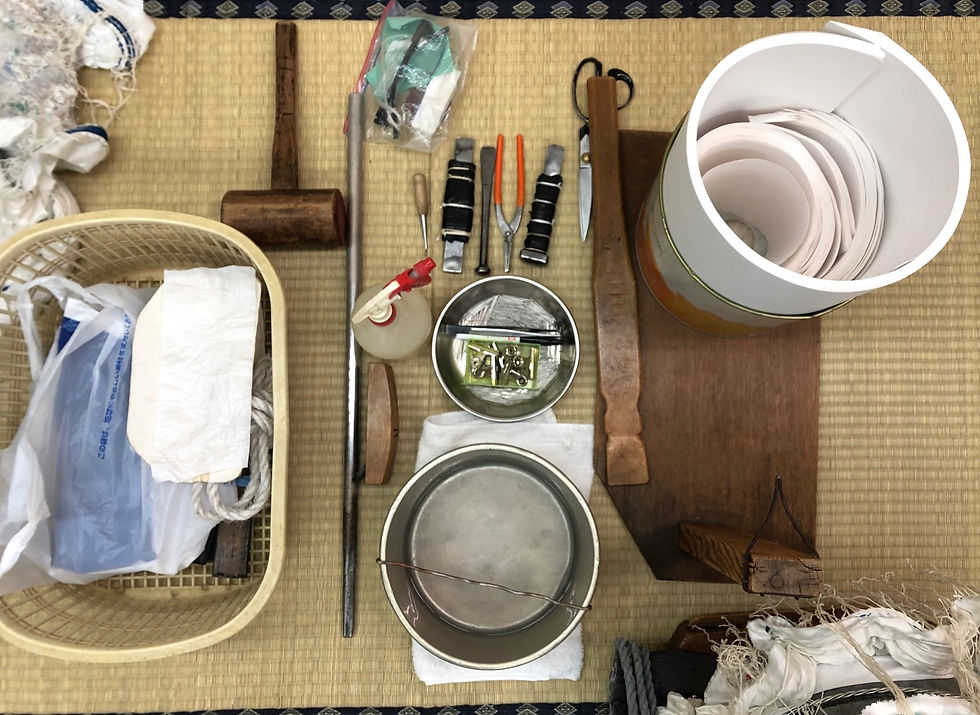

Before stating the shibori work, the tub body and lid are scraped with a plane and adjusted so that both joints are snug.
Paper is placed on the edge of the tub to keep the fabric from getting stained or damaged.

The needle is driven along the dyeing line.
In the past, iron needles were used, but now, custom-made stainless steel needles are used.

When finishing the driving needle work, the prepared paper called 'Tsume-gami' () is placed on the part where the fabric was not placed to remove the steps.
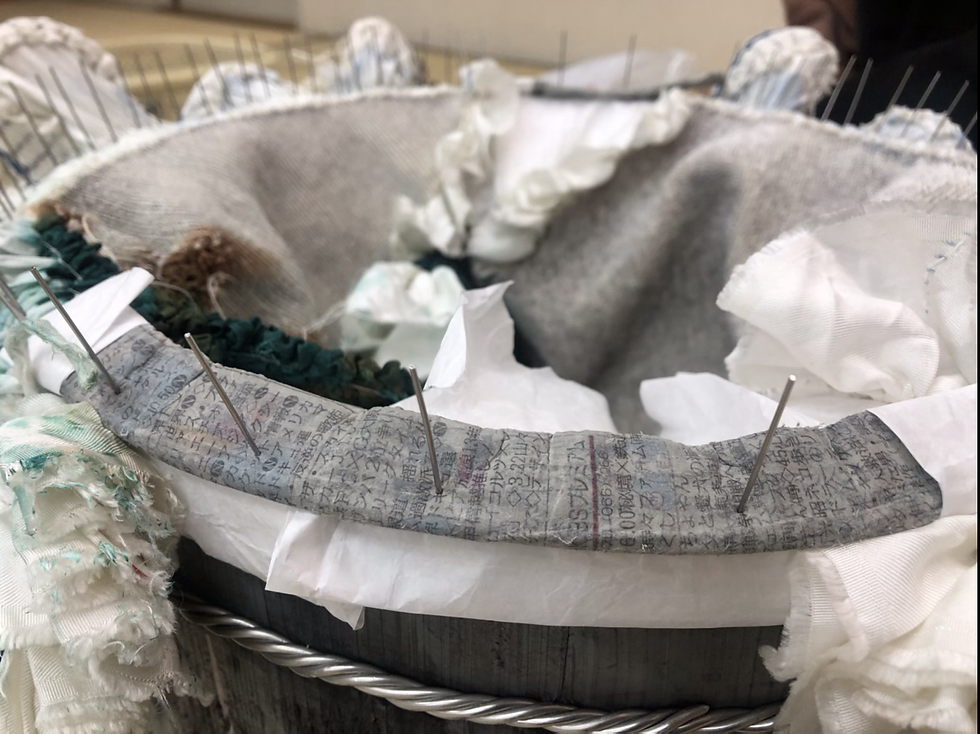
And paper is placed around the edge of the tub again and the lid is closed.
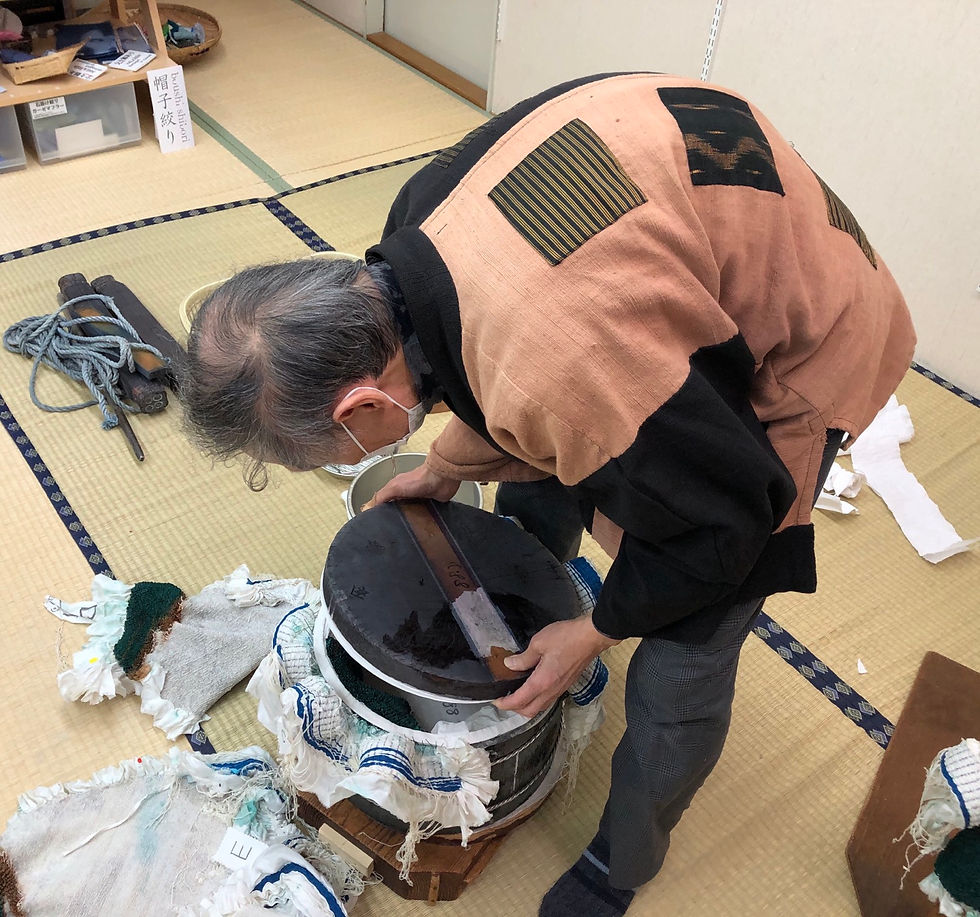
The top and bottom of the tub are sandwiched between strong and thick wood, and both are temporarily tightened with linen rope using a wooden flat bar made of oak called 'shime-gi', driven needles are pulled out, and the dyeing line is adjusted and checked again.
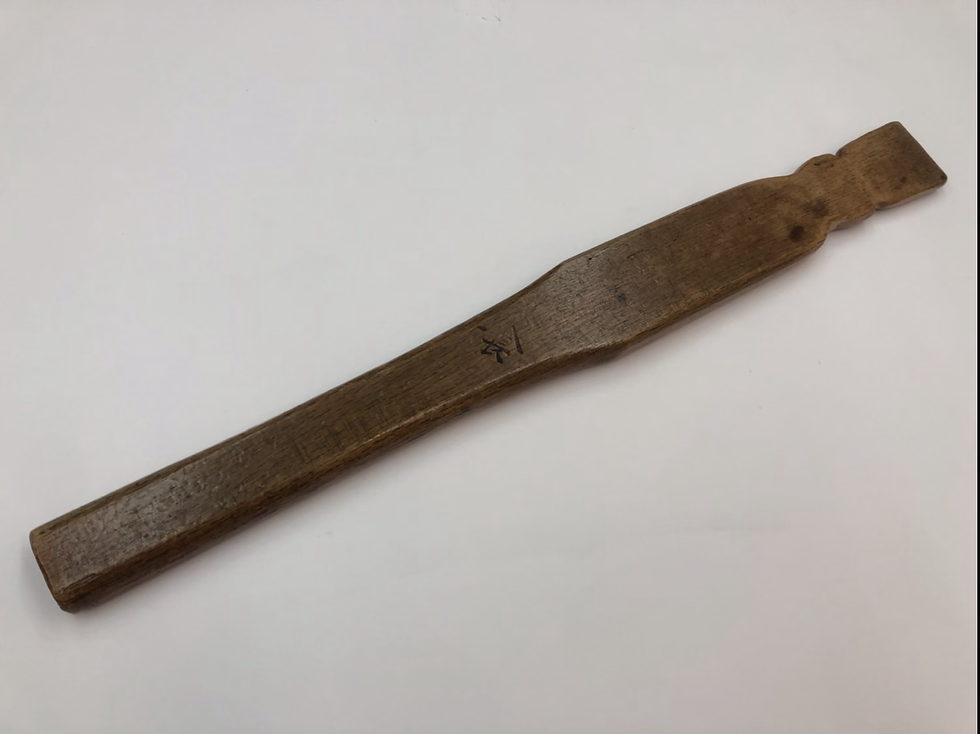
Mojikiri process:
The linen rope is tightened by the principle of leverage using 'Moji-take' (plate-shaped bamboo of about 20cm) and 'Kanateko' (an iron pole) .
Wetting the linen rope with a spray bottle prevents it from suddenly breaking.
If too much pressure is applied to tighten only one side, the position of the lid will shift or the shape will collapse, ruining the work up to this point, so it is important to adjust the tightening strength delicately.
It is a work that requires physical strength, but the linen rope must be tightened carefully.
After the mojikiri process, iron spatulas of various sizes are used to do the komi process (paper is filled between the tub body and the lid), the final adjustment of the dyeing line, and the whole process of oke shibori is completed.


We asked Mr. Nagatani san about the best part of oke shibori.
'Well, after all, when it's dyed, the moment you open the lid of the tub, and when you could see the dyeing line is appearing so neat without any dye leaking, it is the best feeling.'
The shibori process is all a division of labor. The tub is sent to the dyeing craftsman and proceed to the dyeing process.
Comments